Friday, September 29, 2006
I was at Costco this afternoon and happened to see a vendor selling solar panels. I started talking to Dru Sutton from RecSolar about kWatts and costs. I told him I'd send him my historical electricity consumption and some PDF's with elevations and site plans so he could help me figure out what sized system I would need and where it should be located.
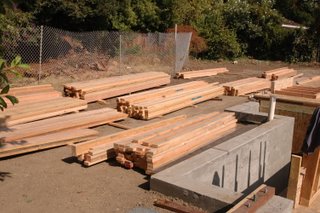
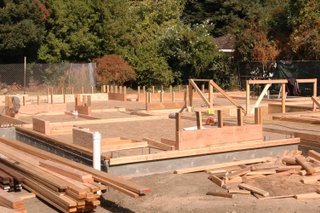
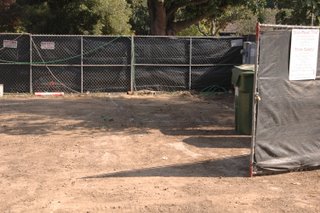
Meanwhile, the carpenters from KC Construction have been busy laying out the sole plates and putting together the headers and cripple studs for all the doors and windows of the first floor.
The third picture shows where Brad's trailer/office will be located, on the right side, in the front of the property.
We stopped by the job site this morning and saw Brad there. It turns out there were a couple of questions for us so it was good that we happened to be there.
1. Brad was concerned the sill height of the window in the craftroom may not meet the egress requirements. It was very close -- within about 1/2", so rather than take any chances, I called up Chris at Argonaut Window & Door and asked him to change that window to a taller one.
2. The structural drawings put a beam right in the middle of one of our pocket doors. After talking with Brad and Rick (from KC Construction), we decided to change the pocket doors to french doors, and we decided to add a 2' long half-wall for the door to open against (sorry Gary).
1. Brad was concerned the sill height of the window in the craftroom may not meet the egress requirements. It was very close -- within about 1/2", so rather than take any chances, I called up Chris at Argonaut Window & Door and asked him to change that window to a taller one.
2. The structural drawings put a beam right in the middle of one of our pocket doors. After talking with Brad and Rick (from KC Construction), we decided to change the pocket doors to french doors, and we decided to add a 2' long half-wall for the door to open against (sorry Gary).
Thursday, September 28, 2006
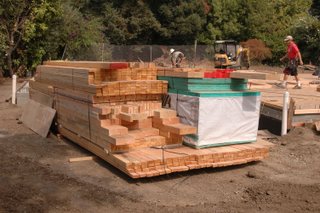
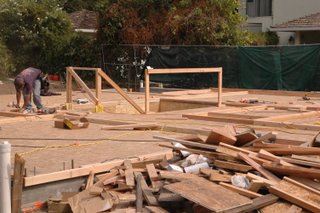
We met with both Brad and Gary at the job site this afternoon and looked at the framing in the basement. We noticed a couple of things that needed to be corrected: the jamb around the sliding door in the workout room needed to be fixed, and a header needed to be added for the built-in cabinet under the stairs. We also spent some time discussing the window seat and the fireplace in the living room. We had been leaning toward a Regency P42 fireplace, but Gary persuaded us to choose a smaller one because the P42 is too large for our modestly sized living room. We'll probably choose either the P36 or P33 model from Regency.
We showed Brad the sample of travertine tile. He told us we could use thinner (less expensive!) tiles, so we'll go find another sample.
Also Brad told us that when we select the toilet for the basement, we'll need to find one that has a 10" rough-in (oops).
And finally, Brad said his trailer/office will be delivered on Monday!
Wednesday, September 27, 2006

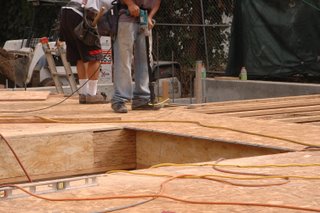
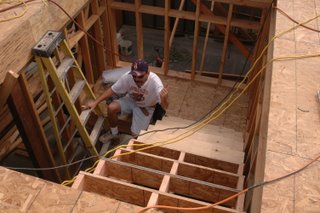
They have also been building the stairs. Once they are done it will be much easier (and safer) to access the basement.
Today we went to Peninsula Building Materials to purchase a beige colored travertine tile sample. We'll use this material for the lower courtyard as well as the back patio.
Also, this morning I got an email from Paul at Adanac Fire Protection with a quote for the sprinkler system.
Monday, September 25, 2006
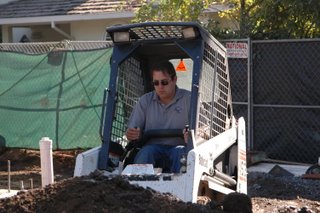
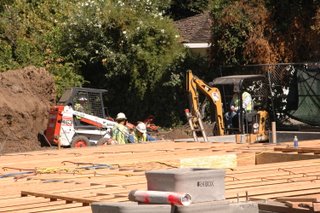
The building inspector came out at about 2 PM today to look at the basement framing and the joists. He gave his approval so KC Construction can proceed with the subfloor and the first floor framing.
Brad and Rick (from KC Construction) were working on the details for pouring the garage slab. They need to slope the concrete so they were checking with the structural engineer to make sure the extra thickness won't be a problem. Rick was told by the structural engineer that the back of the garage must not exceed a thickness of 5-1/2" and the front of the garage must be at least 3" thick. That gives Brad the 2-1/2" he needs to for the slope.
I went down to see Chris Pieper at Argonaut Window & Door to pay the 50% deposit for our Andersen Windows. He'll coordinate with Brad to figure out when the order needs to be placed and when to schedule the delivery. I also asked him to give us a quote for a Jeld-Wen fiberglass front door.
Today, I also talked to Pete Handy at West Coast Insulation Inc. I told him that we're interested in the Regency P42 fireplace and that Brad wants to talk to him about having them do the insulation too.
Finally, I put in a call to Paul at Adanac Fire Protection to find out more about fire protection systems and start him working on a quote for us.
Friday, September 22, 2006
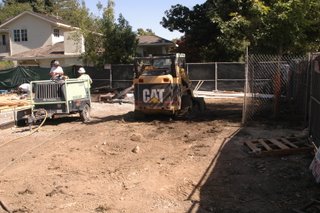
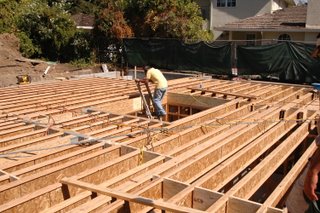
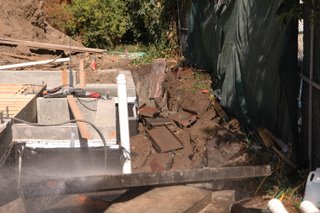
The next thing you will notice is the floor joists are almost finished! Kevin Capps, the owner of KC Construction (the framing contractor), happened to be there. He told me he asked Brad to schedule an inspection for Monday. Kevin hopes to put in the subfloor on Monday after the inspection and finish the first floor framing by next Friday!
Finally, you will notice that Ferma has removed the tops of the steel beams from the retaining walls on the left and right sides of the property. Just the top few feet were removed. The remainder of the steel beems and wooden slats -- everything below two feet from the site grade -- will be left in the ground forever.
This afternoon we went to West Coast Insulation, Inc. and met with Pete Handy. He showed us various models of fireplaces and gave us a bunch of brochures to look at. On his suggestion, we're leaning toward a Regency model, possibly the P42.
Thursday, September 21, 2006
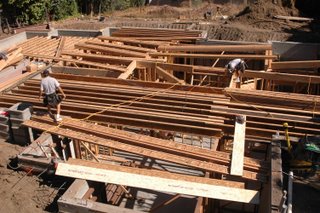
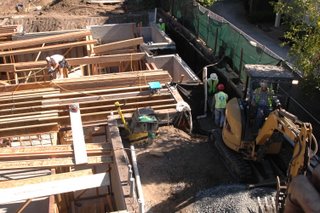
Ferma Corporation was also working hard to backfill the sides of the foundation. They have to work carefully in a confined space, using wheel barrels to move the rocks and dirt.
I've double checked the revised window quote from Argonaut Window & Door. Everything looks okay so I just need to fax it back to Chris.
Wednesday, September 20, 2006



I talked to the field foreman from Ferma, and he said they will be removing the Baker tank on Friday.
The framing contractors from KC Construction were also there, putting in the joists. You can see all the piles of lumber that had been craned onto the tops of the basement walls yesterday.
I called Brad while I was at the site, and he said the inspector was there this morning. We passed the inspection, so Jim Giancola Concrete can pour the stairs and the planter box in the lower courtyard.
Tuesday, September 19, 2006
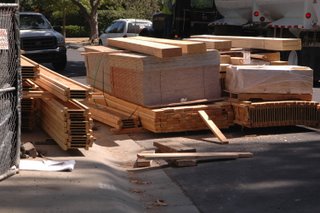

There was lots of activity today with three different groups of subcontractors present at the site.
Ferma Corporation was there, working on the backfill. The last couple of days, they had been pulled off our job by an emergency, so they were busy making up for lost time. One problem they need to solve is how to get the rocks and dirt to the back of the property -- there's no room for them to maneuver on the sides of the property (it's too narrow). They may have to bring in some sort of conveyor machine to shoot it across to the back.
The crew from Ferma was also cleaning out the Baker tank -- there was about six inches of sediment in the bottom. They are hoping to remove the Baker tank by tomorrow.
The framing contractors from KC Construction were also there, finishing the framing in the basement. A load of lumber for the floor joists and subfloor was delivered this morning. Brad brought in a crane later in the afternoon to move the joists into place for the carpenters, but it had to wait. Ferma had to move some of the dirt out of the way so the crane could get in there.
I also met Jim Giancola (from Jim Giancola Concrete) for the first time. He happened to be meeting a potential client at our job site. His crew was busy finishing up the forms in the lower courtyard. An inspector is coming out tomorrow, before they pour the concrete for the stairs and the planter box.
Monday, September 18, 2006
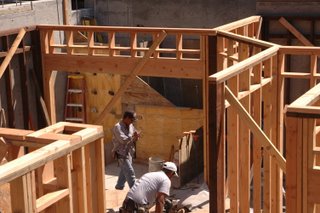
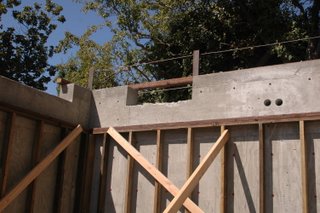
I noticed that a notch had to be cut into the concrete wall for the side yard door leading out of the garage -- as seen in the second picture (oops).
I need to talk to Brad about the window order before we place it. I think some of the basement walls have been framed differently than expected (2x6 vs. 2x4 construction) so we may need to adjust the order for the jamb extensions.
I don't think Ferma Corporation was on site today. As of late this afternoon, the Baker tank was still there (bummer).
Thursday, September 14, 2006

All of the sump pumps have been turned off. Ferma Corporation will be coming back on Monday to remove the Baker tank, which is completely empty. And they'll be finishing up the backfill throughout that week. This is great news for Brad because soon he'll have a place to put his office.
Brad told us we need to call Chris at Argonaut Window & Door to order the windows. Brad will be needing the windows in about eight weeks and there's a four to six week lead time for them.
Brad is pushing us to decide on the hardscape for the lower courtyard. He needs to know the thickness because that affects the spacing of the steps. He also needs us to decide on the front door and the fireplace for the rough opening sizes.
Tuesday, September 12, 2006
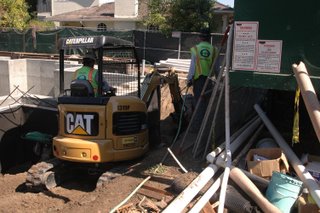
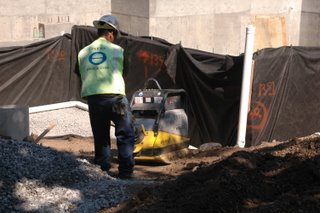
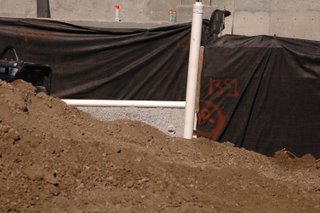
They also started installing the perforated PVC pipe over a bed of crushed rocks. As you can see from the pictures the pipe and rocks are wrapped with filter fabric to keep sediment from getting into the pipe and clogging it.
Monday, September 11, 2006
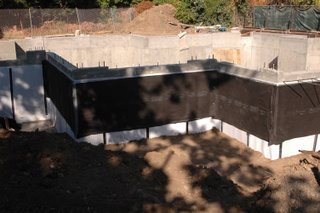

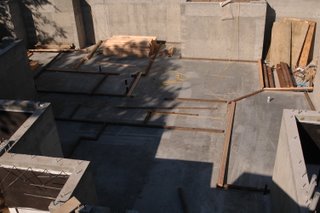
Large piles of lumber have been lowered into the basement, and the framing contractors have started working on the interior walls.
This last picture was taken from the top of the Baker tank, looking down into the basement.
This afternoon we drove down to Cornelia's again. Michelle gave us pricing information for some of the faucets, toilets, and sinks that we like.
Friday, September 8, 2006
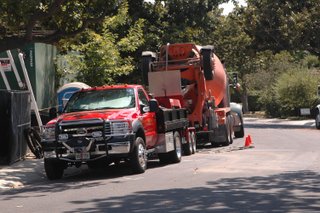
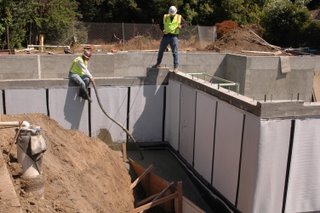
Thursday, September 7, 2006
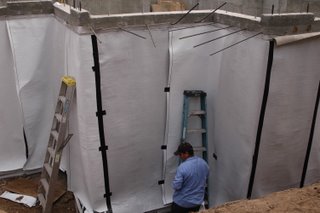
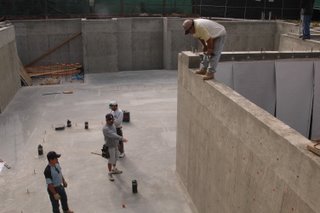
Water- proofing Associates was putting the finishing touches on a layer of Ultraseal.
Jim Giancola Concrete had a worker walking the top of the walls, straightening out all of the hold downs. And there was another worker gettting ready to grind down and smooth out some of the concrete at the base of the walls.
And finally there was another crew (probably the carpenters) snapping chalk lines for the walls.
Tuesday, September 5, 2006
Brad sent me an email today saying they took some core samples from the walls. It tested to 2,910 lbs which is great. I suspect the reason they took samples from the walls is because the day-14 sample that was cast when they poured the walls, did not test very well.
Brad is going to move forward with the waterproofing of the walls and will pour the backfill on Friday.
Correction and update on 9/14/2006:
Brad told me today that the core samples were tested at 2,560 and 2,610 lbs by Granite Rock. The reason why core samples were taken was because the day-14 sample tested to only 1,710 lbs by DCI. Brad said he wants to test the remaining two cast samples at DCI to verify the results obtained by Granite Rock.
Brad is going to move forward with the waterproofing of the walls and will pour the backfill on Friday.
Correction and update on 9/14/2006:
Brad told me today that the core samples were tested at 2,560 and 2,610 lbs by Granite Rock. The reason why core samples were taken was because the day-14 sample tested to only 1,710 lbs by DCI. Brad said he wants to test the remaining two cast samples at DCI to verify the results obtained by Granite Rock.
Subscribe to:
Posts (Atom)